We guide towards logistical and financial benefits. By combining proven methodologies and innovative solutions, we guide our clients to go one step further into continuous improvement and the facilitation of the reorganization.
Visualizing, quantifying and optimizing flows and processes within a factory in digital ways are catalysts for change and a very efficient way to pave the road to transformation. Nevertheless, planning alone does not lead to change. It takes blood, sweat and tears, behavioral adaptations, consensus building and most importantly, the ability to put the theory into practice.
By successfully achieving considerable transformations for our clients all the while using our software, we gained the necessary experience in project implementation as well as project and change management to develop our consulting and training activities.

Process
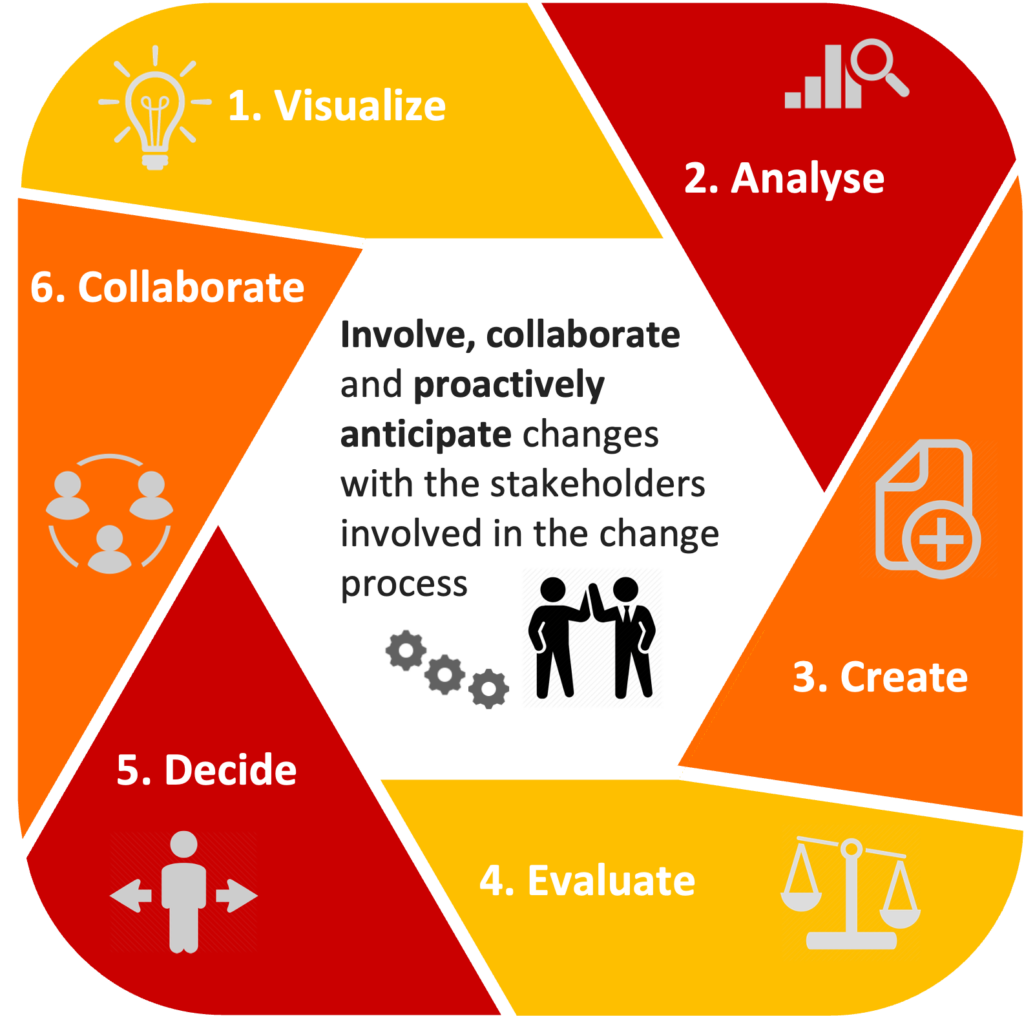
- Visualize flows, factory layouts, and planning setups to validate data, resources, and processes across the entire plant.
- Analyze flows with dynamic spaghetti diagrams, simplifying global analysis using filters and various tools for immediate problem identification. Build machine cells (QRM & Cellular Manufacturing) tailored to product families.
- Create multiple scenarios—either guided by proposed optimizations or manually developed out-of-the-box solutions that integrate real-world expertise.
- Evaluate different strategies through planning simulations and generate dynamic Value Stream Mapping (VSM) to eliminate waste and improve efficiency.
- Compare & Decide collaboratively as a team, selecting solutions that align with your company’s capacities and constraints.
- Continue to collaborate and drive continuous improvement with SIMOGGA Solutions.

Empower Your Production with SIMOGGA Solutions
- Enhance Collaboration among all stakeholders in both the change process and production operations
- Accelerate Decision-Making and improve operational agility by reducing planning and management time
- Engage Operators in designing solutions that benefit the entire facility
- Enable Faster Problem Identification and effortless solution development
- Reduce Factory Workload & Traffic by structuring product families and machine cells
- Increase Responsiveness to Market Demands and enhance on-time delivery performance
- Provide a Complete Toolbox tailored to diverse working methods, fostering innovation and ideation
- Optimize Throughput, Resource Utilization, Lead Time, and WIP, minimizing waste and maximizing efficiency

Human Benefits
- Easy to Use & Team-Oriented – Designed for seamless adoption and involvement of all stakeholders.
- Intuitive 2D Visualization – Simplifies understanding and enhances decision-making across teams.
- Accelerates Decision-Making – Facilitates faster, data-driven choices while boosting collaboration.
- Supports Change Management – A collaborative approach to drive smooth and effective transitions.
- Simplifies Problem Identification – Enables quick assessment and development of tailored solutions.
- Enhances Agility – Adapts to variability in resources, products, demand, and investments.
- Optimizes Costs & Resources – Saves capital investment, time, and operational costs.
Operational Benefits
- Dynamic Spaghetti Diagram – Analyze thousands of product flows with a single click.
- Instant Value Stream Mapping (VSM) – Get real-time insights into processes and waste reduction opportunities.
- Bottleneck Detection & Resolution – Identify constraints and implement solutions to enhance efficiency.
- Comprehensive Site Overview – Gain a global view of flow, efficiency, throughput, and capacity under material and human constraints.
- Waste & Cost Reduction – Minimize waste, costs, lead time, and work-in-progress (WIP) for streamlined operations.
- Real-Time KPI Assessment – Instantly evaluate key performance indicators for informed decision-making.
- Multi-Scenario Analysis & Dashboards – Compare different alternatives to select the best strategy for your operations.
